A cooling tower is an industrial installation designed to cool circulating water used to remove heat from process equipment in circulating water supply systems. Cooling towers play a critical role in various industrial processes, ensuring the efficient operation of equipment and maintaining optimal production output. They are widely used in industrial enterprises, nuclear power plants, and thermal power plants. Despite their efficiency, cooling towers are complex technical devices requiring experienced electro mechanical company for maintenance and repair.
Classification of Cooling Towers
Cooling towers can be classified based on several criteria, with the most common being the method of air supply:
- Tower Cooling Towers: These use a high exhaust tower to create thrust for air movement. The tall structure enhances the natural draft effect, pulling air through the system without the need for mechanical fans.
- Ventilatory Cooling Towers: In these towers, mechanical fans create the necessary thrust, forcing air through the system. This design allows for greater control over airflow and cooling capacity, making them suitable for a variety of industrial applications.
- Open (Atmospheric) Cooling Towers: These utilize the power of wind and natural convection as air moves through the sprinkler system. They rely on natural weather conditions, making them less predictable but highly energy-efficient under optimal conditions.
- Ejection Cooling Towers: These leverage the ejection effect, where a water-air mixture moves at high speeds through special channels. The ejection effect increases the contact surface area between water and air, enhancing cooling efficiency.
- Splashing Cooling Towers: These operate on the principle of simple spraying or fountain mechanisms. Water is distributed through nozzles, creating droplets that increase the surface area for heat exchange.
- Dry Cooling Towers: These are essentially radiators where cooling occurs without evaporation of the cooled medium. They are sectional prefabricated structures, each section being a radiator made of finned pipes and a fan with an asynchronous motor. This design is beneficial in water-scarce environments, as it reduces water consumption.
Types of Cooling Towers
Ejection Cooling Towers
Ejection cooling towers are capable of handling the highest hydraulic loads and can cool water with a large temperature drop, up to 90 °C. This efficiency is due to the absence of a sprinkler and the large total surface area of fine droplets combined with high-speed water-air flows. Energy costs for these systems, with proper water supply and automation, are comparable to those of standard fan installations. Additionally, ejection cooling towers are frost-resistant, making them highly economical in areas with cold winters. Their robust design allows them to operate efficiently in harsh climatic conditions, ensuring reliable performance year-round.
Energy Towers Based on the Maisotsenko Cycle
The Maisotsenko cycle is applied in energy towers to improve cooling efficiency, especially in power plants. Cooler water enhances condensation in chemical and energy devices, improving overall efficiency and reducing fuel consumption. The Maisotsenko cycle utilizes a novel thermodynamic process that allows for cooling water below the ambient wet-bulb temperature, significantly enhancing the cooling capacity of the tower.
Efficiency and Applications
Most industrial cooling towers use direct evaporative cooling, where water and air come into direct contact within the device. The efficiency of these towers is influenced by the wet bulb temperature of the cooling air, making them particularly effective in dry climates with low humidity. Despite this, they are also used in regions with higher humidity, though their performance may not be optimal.
Historically, fan cooling towers were considered the most efficient due to their ability to provide deeper and higher-quality water cooling while handling large specific heat loads. However, they require electrical power to operate the fans. The advent of more advanced designs, such as ejection and energy towers, has provided more options for industries seeking efficient and sustainable cooling solutions.
Potential Risks and Maintenance
Cooling towers must be operated and maintained properly to prevent several potential risks:
- Freezing: In cold climates, cooling towers can freeze, leading to operational failures. Ice formation can block water flow and damage structural components, necessitating frequent inspections during winter months.
- Mechanical Stress: Scale formation on internal surfaces can reduce efficiency and increase stress on fan motors and other moving parts. Regular descaling and water treatment are essential to maintain optimal performance and extend the lifespan of the cooling tower.
- Bacterial Growth: Cooling towers can harbor harmful microorganisms, and biofilm formation can clog filters and other components. Routine water quality monitoring and disinfection are crucial to prevent the spread of pathogens like Legionella, which can pose serious health risks.
- Water Vapor Emission: During operation, cooling towers release water vapor at high temperatures (up to 45 °C), which can increase air humidity in the surrounding areas. This can lead to condensation issues and affect local microclimates. Proper drift eliminators can help minimize water vapor emissions.
Preventive Measures
To mitigate these risks, it is essential to follow proper operational protocols and conduct regular preventive maintenance. Involving professional electromechanical companies can ensure that cooling towers function efficiently and safely. Regular inspections, cleaning, and adherence to maintenance schedules are crucial for the longevity and reliability of cooling towers. Implementing automated monitoring systems can also help detect and address issues before they escalate, ensuring continuous and safe operation.
Conclusion
Cooling towers are indispensable in industrial settings for their role in heat removal and process efficiency. Understanding their classification, types, and potential risks helps in optimizing their use and ensuring safe and effective operation. Regular maintenance and professional involvement are key to sustaining the high performance and longevity of these vital industrial devices. By adopting advanced cooling technologies and adhering to best practices in maintenance, industries can enhance their productivity, reduce operational costs, and contribute to a sustainable future.
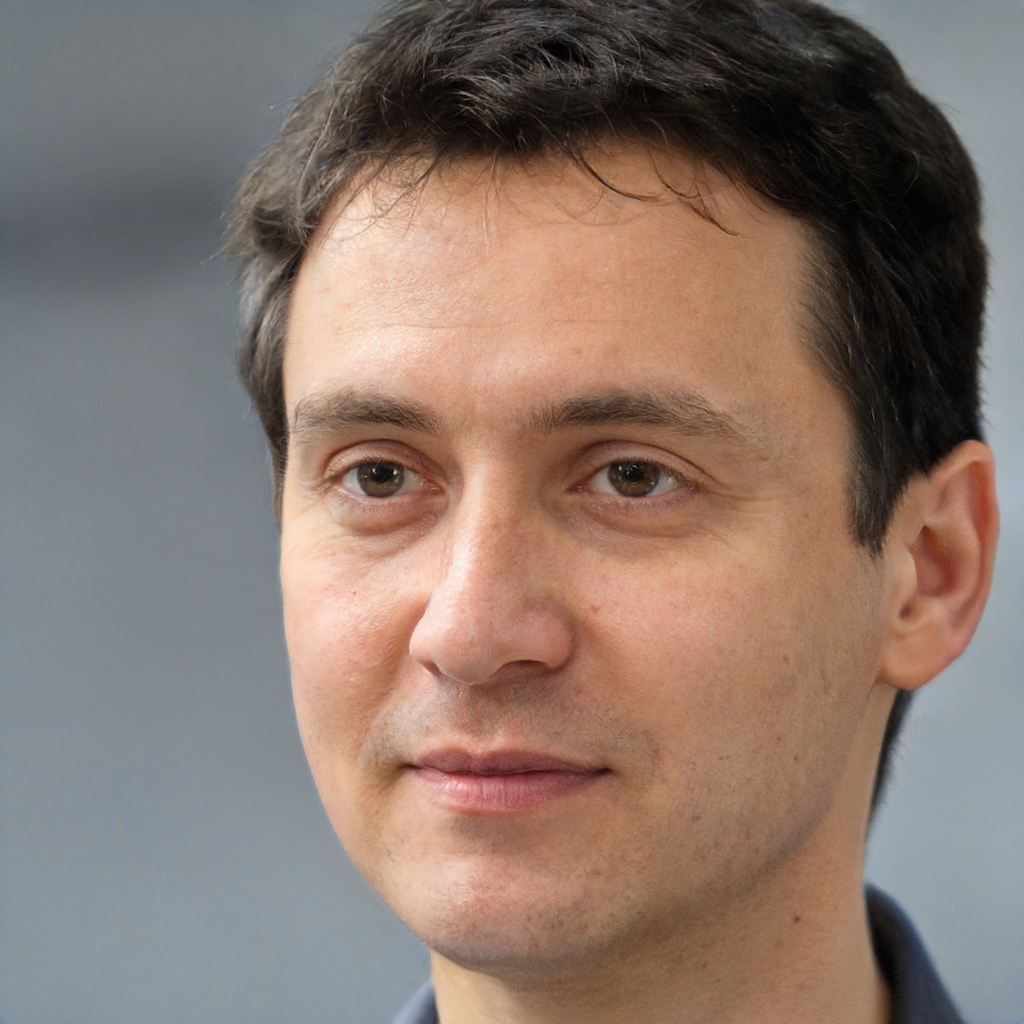
Cyclist, father of 2, fender owner, International Swiss style practitioner and HTML & CSS lover. Working at the intersection of beauty and mathematics to create not just a logo, but a feeling. Check me out on Dribbble or Medium.
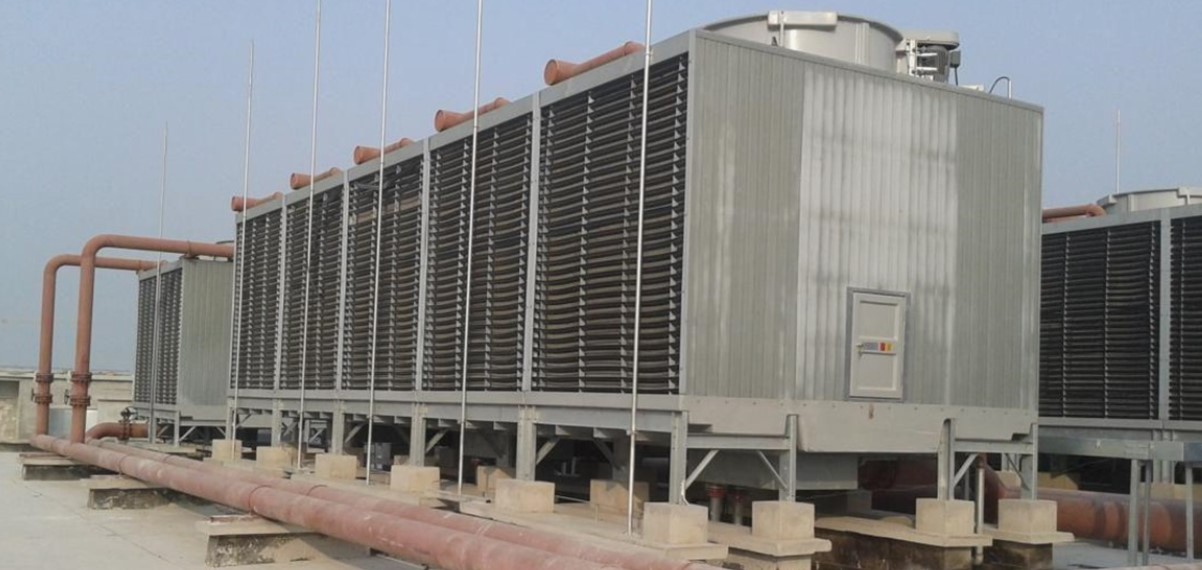